Welcome to a deep dive into one of the most ambitious projects I’ve worked on over the past few years: designing and producing a fully 3D-printed tennis racket. It all began with a simple idea—what if I could create a playable tennis racket using 3D printing technology?
This journey started with me 3D printing smaller components like handles, pallets, and buttcaps. After researching online, I found little evidence of anyone successfully producing and playing with a 3D-printed tennis racket. So, I decided to take the leap myself. At worst, I’d learn a lot about racket design and 3D printing; at best, I’d make history by becoming the first to play tennis with a 3D-printed racket.
In the end, I achieved a playable racket with unique features that showcase the potential of 3D printing. In this article, I’ll share the highlights, technical details, and future possibilities for this project
The First Playtest: On-Court Experience
The first playtest was a significant milestone. I strung the racket with Babolat RPM Power strings (1.25 gauge) at 22 kilos and started with some light hitting to see how it performed. Gradually, I increased the intensity, moving back to the baseline and testing how the racket held up under heavier hitting.
Initial Impressions
- Feel and Flex: The racket felt softer than traditional rackets, largely due to the materials and design choices.
- Performance: Despite being the second iteration, the racket performed better than expected. The power and stability were impressive, but the sweet spot was too low, and the upper hoop lacked stiffness.
- Stringbed Response: Inconsistent stringbed response highlighted the need to adjust the beam thickness ratio and material distribution for future iterations.
- Personal Preference: I found the racket suited my backhand better than my forehand, likely because I was adjusting my forehand grip to a semi-western at the time.
What Stood Out
The racket’s string hole design allowed the strings to move freely, reducing friction and enhancing the ball pocketing effect. This, combined with the softer frame, created a unique feel when striking the ball.
Racket specifications:
Why 3D Print a Tennis Racket?
You might wonder—why use 3D printing to create a tennis racket? Here’s why this technology is a game-changer for racket design and manufacturing:
- Unmatched Design Freedom:
- 3D printing allows for the creation of complex geometries and innovative features that are difficult or impossible to achieve with traditional manufacturing.
- Rapid Prototyping and Iteration:
- Prototypes can be quickly adjusted and reprinted, accelerating the development process.
- Customization and Personalization:
- Specifications like weight, balance, swing weight, beam thickness and grip shape can be tailored to individual players on demand.
- Sustainability:
- 3D printing minimizes waste, reduces post-processing, and eliminates the need for environmentally harmful materials like carbon fiber and resin.
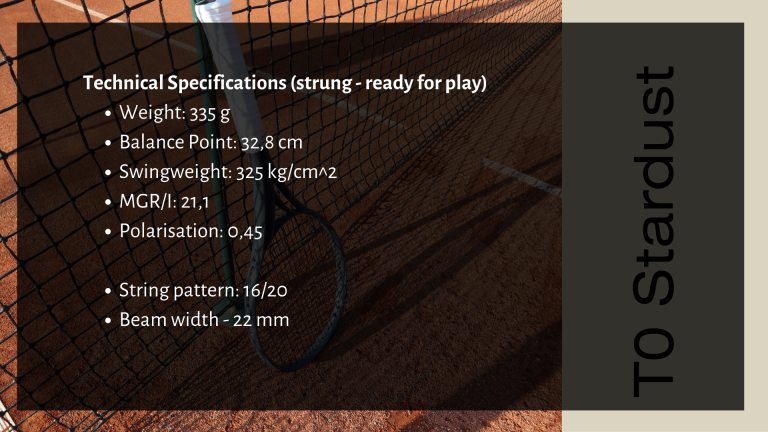
Design Highlights of the T0 Stardust Racket
1. X-Throat Design
The most distinctive feature is the X-Throat Design, which adds a unique aesthetic while improving performance. It enhances torsional stability and reduces throat flex, particularly in directions crucial for spin production.
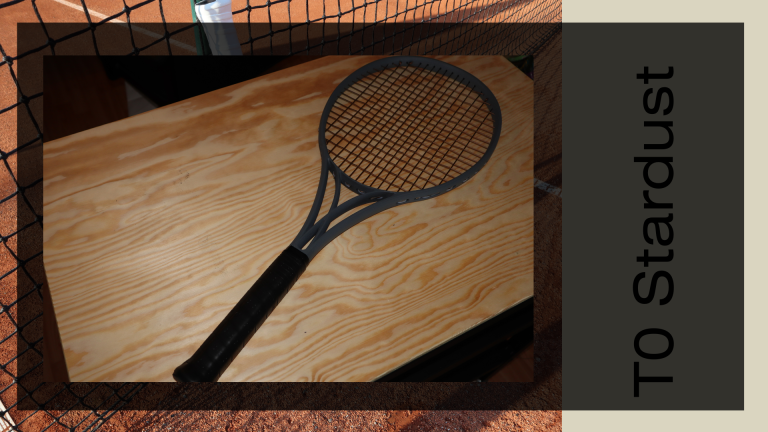
2. Rounded String Transitions and Oval String Holes
I incorporated rounded transitions and oval-shaped holes where the strings pass through the frame. This reduces friction and enables freer string movement, eliminating the need for traditional plastic grommets.
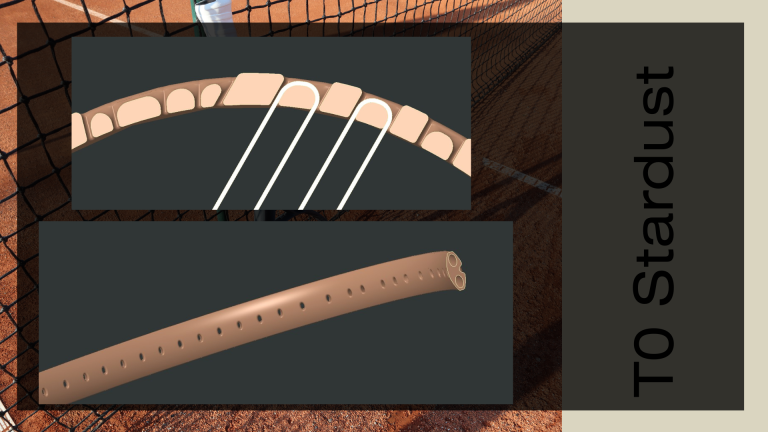
3. Twin-Tube Frame Design
To improve the weight-to-flexural strength ratio, I experimented with a twin-tube frame design. However, this resulted in layer shifting during the 3D printing process, which ultimately caused cracks along the shifted layers. In the future, I plan to replace this with a full-beam frame and optimize material distribution with the use of minimal infill and varying outer layer thickness for greater durability.
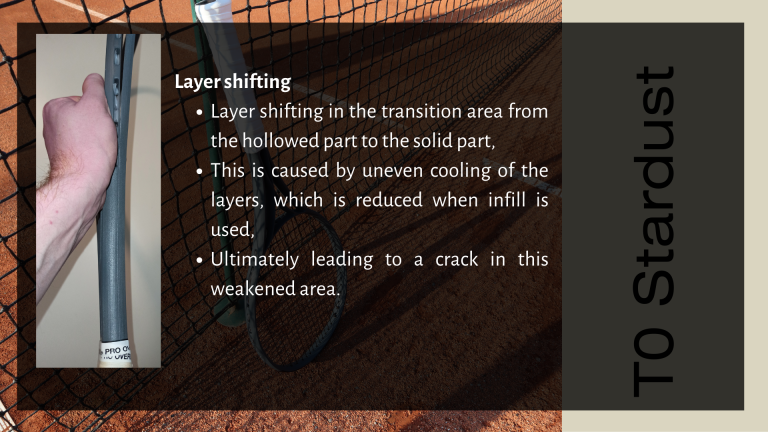
4. Brick-Layer 3D Printing Configuration
To prevent cracks along layer lines, I’m exploring a brick-layer printing configuration. This approach offsets each layer slightly, creating an interlocking structure that enhances durability and strength.
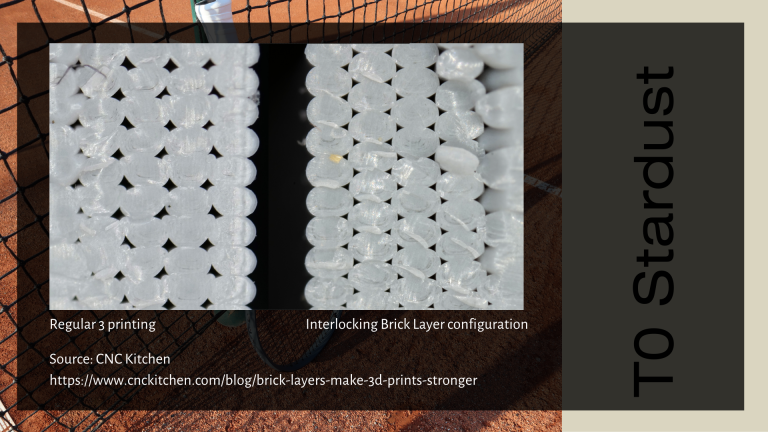
5. String Channel Redesign
I replaced traditional grommet channels with individual string hole connection channels, giving the racket a cleaner aesthetic. These channels are coated with a Teflon film, reducing string friction and enhancing string movement.
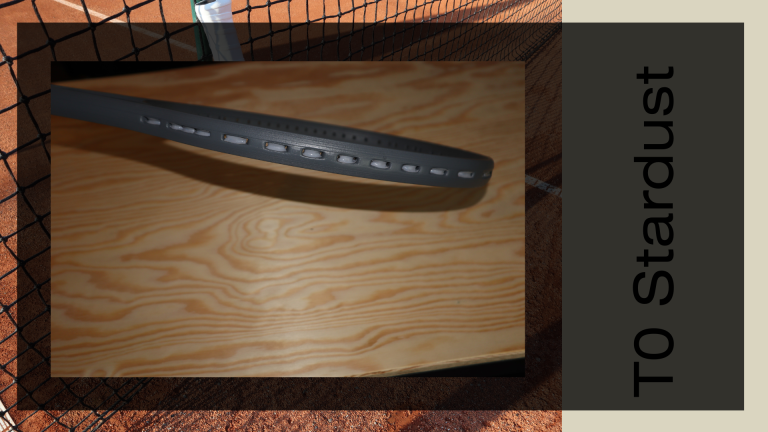
Material Selection: Raise3D Hyper Core PPA CF25 Filament
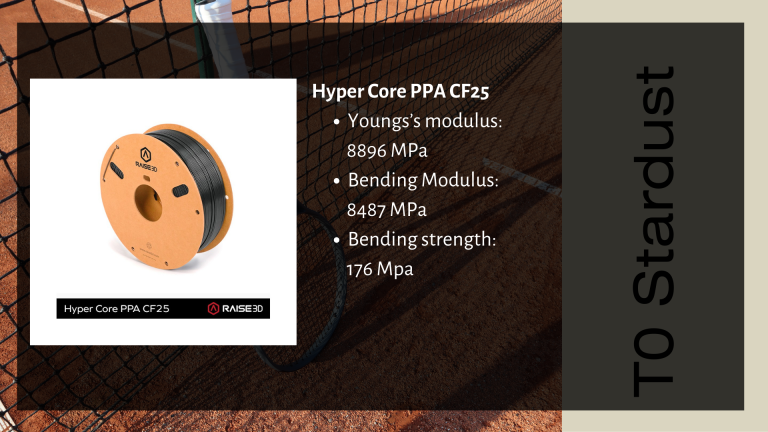
For this project, I used Raise3D Hyper Core PPA CF25 filament. This material was chosen for its:
- High Bending Modulus and Strength: Critical for stability during play.
- Carbon Fiber Core: The 25% carbon fiber core provides the increased bending modulus and because only the core has filaments, this provides better layer adhesion.
While this material performed well, future iterations could benefit from continuous carbon fiber 3D printing, which co-extrudes continuous fibers for better strength and stiffness.
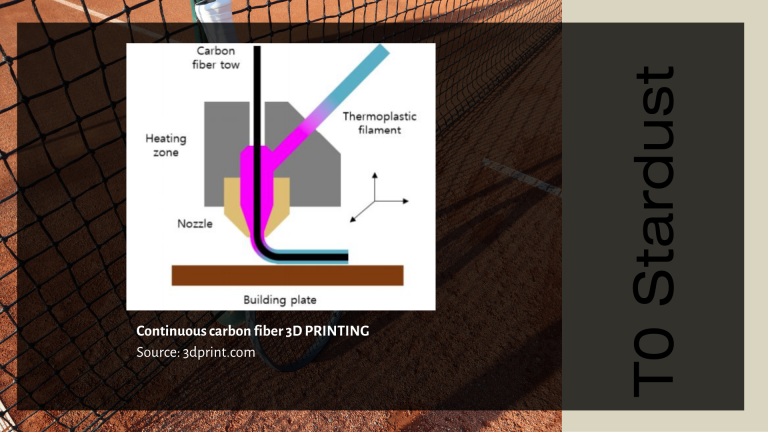
The Future of 3D Printing in Tennis Racket Design
The potential of 3D printing in tennis is enormous, especially with advancements like continuous carbon fiber deposition. Unlike traditional filaments with short fibers, this technology co-extrudes continuous fibers with the base material, delivering higher strength and stiffness. Although I couldn’t use this method for the T0 Stardust, it’s an exciting frontier for sports equipment manufacturing.
Key challenges include:
- Production Time: Current 3D printing processes are slow, making mass production challenging.
- Material Advancements: While continuous fiber printing is promising, it’s still in its infancy and requires further development for widespread use.
Future Improvements for T0 Stardust
Here’s how I plan to refine the racket design and bring 3D-printed tennis rackets closer to mainstream adoption:
- Increase beam thickness for greater stiffness.
- Replace the twin-tube design with a full beam and optimized infill.
- Implement brick-layer 3D printing for enhanced durability.
- Explore continuous carbon fiber 3D printing.
- Integrate proprietary design improvements to elevate performance further.
Closing Thoughts
The T0 Stardust Project is a testament to the possibilities of 3D printing in tennis equipment. While this is just the beginning, the results so far have exceeded my expectations and opened the door to even more innovation.
One thought on “Project T0 Stardust – The first 3D-Printed Tennis Racket”
Comments are closed.